Lean Six Sigma Certification
Demonstrate your ability to apply the principles and tools of Lean Six Sigma through Certification.
"Certification is the formal recognition and acknowledgment that a person has demonstrated appropriate understanding and effective, practical application of Lean Six Sigma methodology and key concepts and tools. The act of becoming Certified demonstrates that this person has delivered tangible, measurable improvement and is able to perform at a high level of excellence both personally and within their organization".
PROFESSIONAL ACCREDITATION
Certification Components
Earn Your Lean Six Sigma Accreditation in Three Steps
01
Education
The first component is to attain the Lean and/or Six Sigma Body of Knowledge by completing a Lean and/or Six Sigma training program.
This training can be completed by training for Individuals, training for Team, self paced online learning or with proof of training from another institution.
02
Theoretical Knowledge
Following the training, the Certification Exam assess the extent of theoretical knowledge.
Exams range from 35 to 70 questions depending on the Body of Knowledge being tested. The exam is administered online and pass mark for all Certification Exams is 70%.
03
Practical Application
The third component is to demonstrate a practical application of the Lean and/or Six Sigma tools and methodology by completing and submitting a completed project or improvement event for review.
Depending on the level of desired Certification, the submission is either a 'project' or an 'event'.
A Project is defined as having followed the DMAIC (Define, Measure, Analyze, Improve, Control) life-cycle and will include relevant analyses such as Fishbone, Pareto, Hypothesis Tests, Regression etc. where applicable.
An Event is defined as having successfully completed a Kaizen Improvement Event which is adequately documented using the A3 format.
Certification Registration:
LEAN Improvement Events
An Event is defined as having successfully completed a Kaizen Improvement Event which is adequately documented using the A3 format.
Lean Yellow Belt
These events can be one of the following;
- Map an existing process with a team, conduct an FMEA on that process and identify failures modes, and then implement an action plan to address one or more of the failure modes identified.
- Map and document an existing process that is deemed to be "poorly managed" or not "well understood", identify key performance metrics (ex. cycle time, error rates, frequency of request/transaction, etc.) and implement a "control plan" (INCLUDING PROCESS DASHBOARD) that will provide more transparency on the process, ultimately resulting in improved management, less variation, more proactive, less reactive, etc.
- Identify a 5S (workplace organization) opportunity and make it happen, including a post-project audit regimen.
Lean Green Belt
Options for this ‘CI Event’ are as follows;
- Successful completion of a “kaizen” (PDSA/PDCA) project
- 1-5 day event
- focus on localized rapid improvement (5S/6S or root cause/failure mode)
- use of basic tools/methods (see below)
- evidence of benefit/improvement and sustainability
2. Suggested Approach for Non-5S event
- Problem statement (5W2H)
- Project charter (incl. current state, voice of customer, scope, constraints, goals, team, etc
- Process map
- Cause and Effect
- Pareto
- Summary of current state assessment
- Summary of solutions considered and solutions decided upon
- Improvement made
- Verification of benefits
- Sustainability and control plan
DMAIC Projects
A Project is defined as having followed the DMAIC (Define, Measure, Analyze, Improve, Control) life-cycle and will include relevant analyses such as Fishbone, Pareto, Hypothesis Tests, Regression etc. where applicable.
DMAIC Green Belt and Black Belt
These projects should include the following:
- An executive summary which should be 1-2 pages in length and provide a concise and accurate account of the project
- Define Phase
- Cost of Poor Quality statement
- Customer Satisfaction (Voice of the Customer) statement
- Financial benefits assessment
- Measure Phase
- Process Mapping
- Identification of the 'Vital Few'
- Data Collection Planning & Execution
- Measurement System Analysis
- Capability Studies
- Process Control
- Analyze
- Causality, Relationships & X/Y
- Hypothesis Testing & other tests
- Improve
- Alternative solutions considered
- Recommended solutions
- Control
- Implemented controls
- Evidence of improvement sustainability
Have more questions about Certification?
Let's connect! We want to help you reach your professional goals.
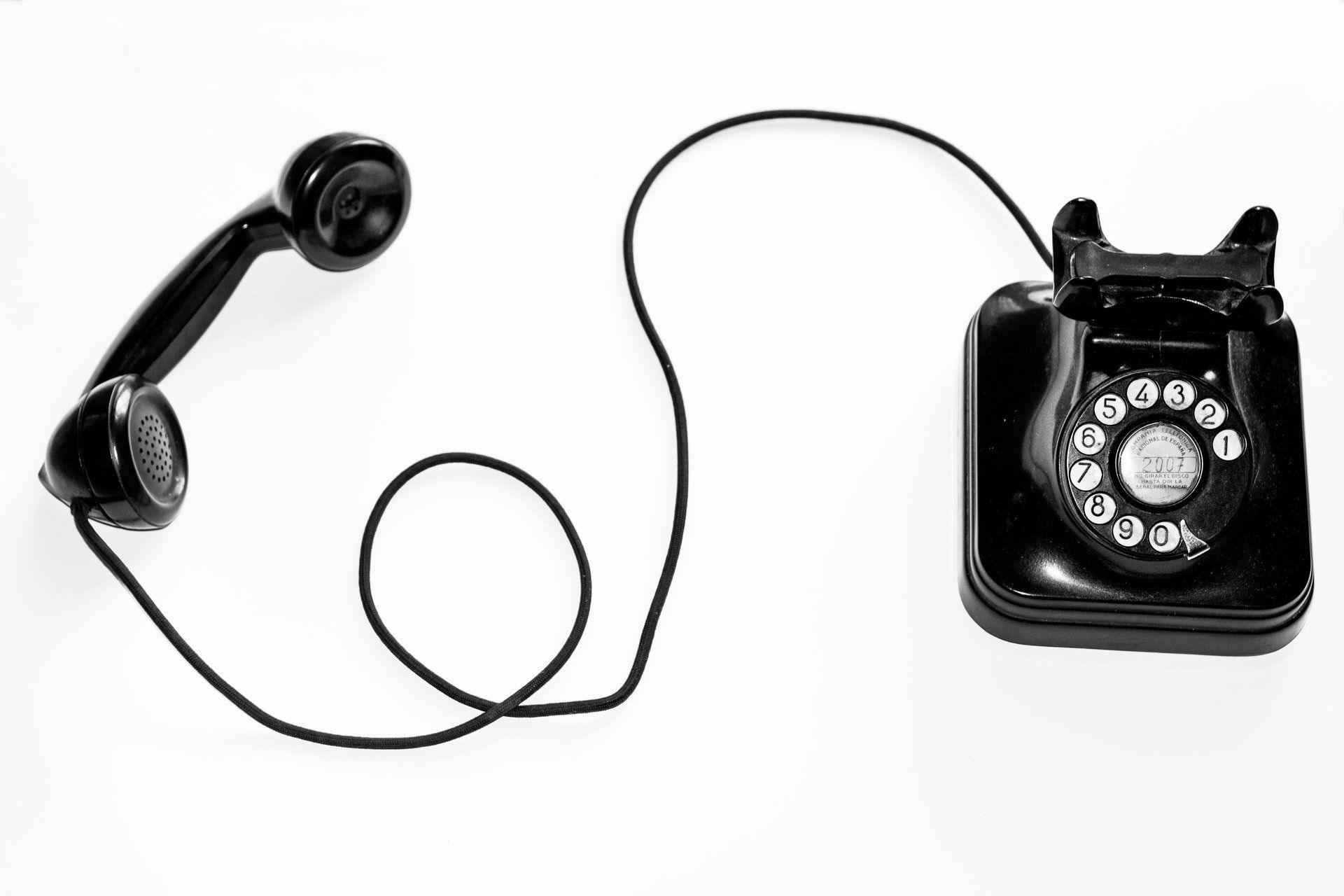
DON'T MISS A THING
We promise to only send you the good stuff.