In Conversation With...
Discussion with Mike Norman, Lean Initiative Specialist

What is your experience with Lean and/or Six Sigma?
In 2005 I was introduced to Lean while in the automotive sector. The company trained Leadership on Lean and the theory of constraints while facilitating small Kaizens throughout the plant to improve throughput. In 2009 I moved to Healthcare and our organization had the opportunity to participate in a Ministry funded Emergency Department wait time initiative. The Leadership Team quickly realized the benefit of using a Lean methodology with positive patient and staff outcomes associated with Lean. This led to an organizational shift in culture to continuously improve on a daily basis while making Lean part of the framework for organizational strategy. Over the years I have been privileged to be coached and mentored by CEO’s, Vice Presidents and expert consultants of various organizations helping to lay the foundation that allows Lean to be front and center in organizational strategy.
What are the top 2 benefits you've seen since embarking with Lean and/or Six Sigma? (culture, moral, customer experience, finance?)
I would have to say that employee engagement has to be the top benefit I have seen and experienced with a culture of Continuous Improvement. As an organization matures with Lean, employee engagement is not only vital but very rewarding to see all of the outcomes associated with improving services. The second benefit would be structure. Using a Lean approach allows an organization to focus from a top down, bottom up approach. Leadership setting the direction while employees are given the knowledge and tools to deliver on the expectations while improving service delivery. Using visual management to be transparent and to turn problems into opportunities.
What are the top 2 biggest challenges?
Buy-in and sustainability. Having a common understanding and message from Senior Leaders throughout the entire Leadership team is critical. In no way do I mean to sound like this is a challenge rather a necessity. What Lean is and isn’t how we transition into a culture of continuous improvement and most importantly the why. Having the buy-in and commitment from Leadership is what I believe is the first step in creating the behaviour, habits and culture of continuous improvement. Lean cannot be one more thing off on the side of your desk and in some cases, Leaders think Lean is the silver bullet that transforms an organization into greatness. When people truly embrace and commit to Lean the improvements and sustainable gains are endless.
What are your best practices for getting people engaged in this cultural shift?
At times Lean has gotten a bad rap, often because it’s not done for the right reason or because people don’t have the right information. Having employees know the why and what’s in it for them goes a long way towards buy-in and participation. Engaging the experts at the sharp end of service delivery. Enabling your employees with knowledge tools and techniques to better understand value from the customers perspective and empowering the employees to remove the non-value add and seek perfection.
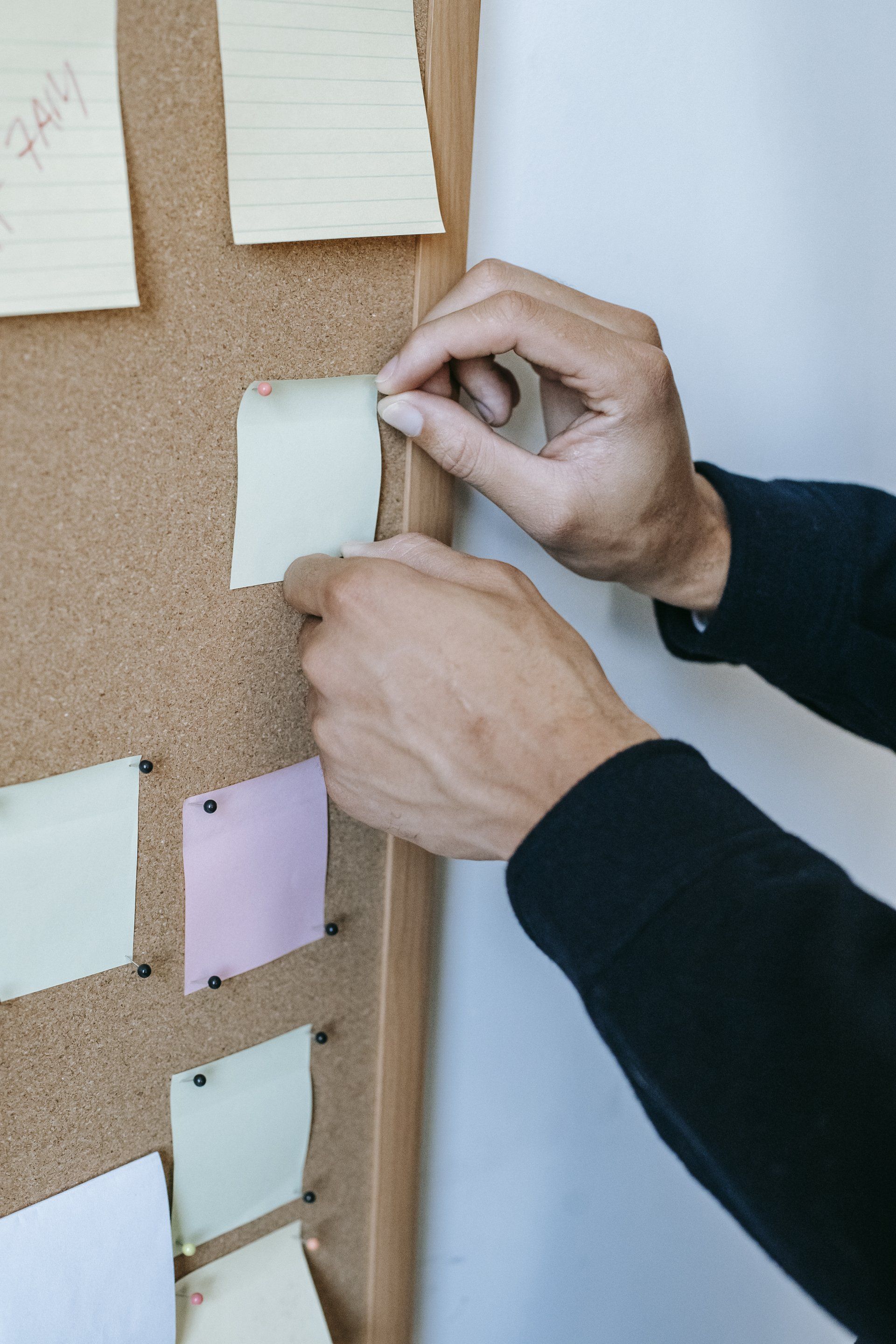